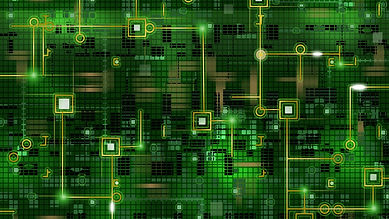
PCB Designing
Printed Circuit Board (PCB) mechanically supports and electrically connects electronic components using conductive tracks, pads and other features etched from copper sheets laminated onto a non-conductive substrate. Components (e.g. capacitors, resistors or active devices) are generally soldered on the PCB.
​
We are here for complete solution for designing PCB(Printed Circuit Board) and provides gateway to learn techniques to design PCB for different kinds of circuits.
​
The electronics circuits are printed on the plate and designed on software.
![]() | ![]() |
---|---|
![]() | ![]() |
![]() | ![]() |
![]() | ![]() |
![]() | ![]() |
![]() |
PCBs can be single sided (one copper layer), double sided (two copper layers) or multi-layer (outer and inner layers). Conductors on different layers are connected with vias. Multi-layer PCBs allow for much higher component density.
FR-4 glass epoxy is the primary insulating substrate. A basic building block of the PCB is an FR-4 panel with a thin layer of copper foillaminated to one or both sides. In multi-layer boards multiple layers of material are laminated together.
Printed circuit boards are used in all but the simplest electronic products. Alternatives to PCBs include wire wrap and point-to-point construction. PCBs require the additional design effort to lay out the circuit, but manufacturing and assembly can be automated. Manufacturing circuits with PCBs is cheaper and faster than with other wiring methods as components are mounted and wired with one single part.
​
A minimal PCB with a single component used for easier prototyping is called a breakout board.
When the board has no embedded components it is more correctly called a printed wiring board (PWB) or etched wiring board. However, the term printed wiring board has fallen into disuse. A PCB populated with electronic components is called a printed circuit assembly (PCA), printed circuit board assembly or PCB assembly (PCBA). The IPC preferred term for assembled boards is circuit card assembly (CCA), and for assembled backplanes it is backplane assemblies. The term PCB is used informally both for bare and assembled boards.
​
Initially PCBs were designed manually by creating a photomask on a clear mylar sheet, usually at two or four times the true size. Starting from the schematic diagram the component pin pads were laid out on the mylar and then traces were routed to connect the pads. Rub-on dry transfers of common component footprints increased efficiency. Traces were made with self-adhesive tape. Pre-printed non-reproducing grids on the mylar assisted in layout. To fabricate the board, the finished photomask was photolithographically reproduced onto a photoresist coating on the blank copper-clad boards.
​
Modern PCBs are designed with dedicated layout software, generally in the following steps:
-
Schematic capture through an electronic design automation (EDA) tool.
-
Card dimensions and template are decided based on required circuitry and case of the PCB.
-
The positions of the components and heat sinks are determined.
-
Layer stack of the PCB is decided, with one to tens of layers depending on complexity. Ground and power planes are decided. A power plane is the counterpart to a ground plane and behaves as an AC signal ground while providing DC power to the circuits mounted on the PCB. Signal interconnections are traced on signal planes. Signal planes can be on the outer as well as inner layers. For optimal EMI performance high frequency signals are routed in internal layers between power or ground planes.
-
Line impedance is determined using dielectric layer thickness, routing copper thickness and trace-width. Trace separation is also taken into account in case of differential signals. Microstrip, stripline or dual stripline can be used to route signals.
-
Components are placed. Thermal considerations and geometry are taken into account. Vias and lands are marked.
-
Signal traces are routed. Electronic design automation tools usually create clearances and connections in power and ground planes automatically.
-
Gerber files are generated for manufacturing.